Ideal Temperature and Environment for Coating Application: Guidelines for Perfect Results
GET A QUOTECALL (770) 722-3486
When it comes to applying coatings, the environment can play a lead role in determining your project's success. Imagine investing time and money into a stunning finish, only for unpredictable weather to sour the results. You wouldn’t let a little rain ruin a picnic, so why risk poor application due to temperature fluctuations or humidity? A smooth, durable coat requires more than just good paint; it needs a thoughtful setup where temperature, airflow, and humidity are all in harmony. Finding that balance can mean the difference between frustration and flawless results. Let’s dive into how you can create the perfect environment for your coating applications.
The ideal temperature for coating application typically falls between 72-74°F, which allows for effective heat loss and generation. Additionally, maintaining adequate airflow is crucial to prevent overheating during the application process, which can negatively impact the quality of coatings.
Essential Conditions for Coatings
The success of any ceramic coating application relies heavily on the interplay between environmental factors like temperature, humidity, and airflow. Each element is vital for achieving a uniform finish while ensuring coatings adhere properly and cure efficiently. Failing to consider these conditions can lead to poor results that compromise both aesthetics and durability.
Temperature and Its Role
When it comes to temperature, aiming for an ideal range of 72-74°F is crucial. Within this narrow band, coatings flow better and bond more effectively. For instance, epoxy manufacturers have observed that divergence from this temperature zone can drastically reduce bond strength. If it's too hot, you risk having coatings dry out before they can set properly; if it's too cold, curing times extend unnecessarily.
In colder conditions—below 50°F, for example—coating products may still work but could yield unpredictable results or take significantly longer to cure. Moreover, one must consider the impact of surface temperatures in relation to ambient temperatures as well. Ideally, surfaces should be at least 5°F above dew point to prevent condensation from forming upon application. When moisture condenses on a freshly coated surface, it can disrupt adhesion and result in mottled finishes—a headache you’ll want to avoid.
Humidity Considerations
Equally significant is the role of humidity in the coating process. Maintaining relative humidity levels between 40-60% strikes a balance essential for optimal adhesion. Higher humidity might create an environment conducive to condensation, hindering proper bonding during application. Conversely, lower humidity levels lead to increased evaporation rates that can dry coatings too rapidly—resulting in cracks or an uneven texture.
Navigating humidity may seem daunting at times; however, devices such as hygrometers can easily help manage this aspect of your environment. An important tip is to monitor the local weather forecast prior to planning your application day. A bit of foresight—and perhaps even rescheduling—can save you from needing repairs or touch-ups later on due to unfavorable outdoor conditions.
Importance of Airflow
Adequate airflow during the application process cannot be overstated. It plays a critical role not only in aiding drying times but also in preventing the buildup of volatile organic compounds (VOCs) released during application. These VOCs pose real health risks if inhaled over long periods without proper ventilation.
Setting up fans or allowing natural breezes through open windows enhances air circulation in your workspace. This mitigates potential respiratory problems and ensures that your workspace remains pleasant while you apply coatings. With these foundational elements firmly established, we can now transition into exploring precise temperature specifications that best suit a variety of scenarios.
Optimal Temperature Guidelines
Achieving perfect results in coating applications hinges significantly on adhering to optimal temperature recommendations. Most coatings flourish between 60°F and 80°F. This specific range isn't arbitrary; it's established through rigorous testing by numerous coating manufacturers. For instance, while applying ceramic coatings, many professionals find that a temperature of around 70°F serves as the sweet spot for proper curing, validated by esteemed brands.
Think of temperature control as a delicate dance, where even the slightest misstep can lead to unfavorable outcomes. If you exceed 85°F, you risk coats drying too quickly, potentially leading to an unpleasant texture or weakening the coating’s durability. In my experience, maintaining moderate temperatures directly influences the finished product. Users who have exceeded recommended temperatures by just 5°F when applying polyurethane coatings discovered a nearly 25% reduction in longevity! Those figures paint a clear picture: Monitoring your environment is not merely a suggestion; it’s essential.
Temperature Control Techniques
To maintain ideal temperatures during application, consider employing climate control systems if you're painting in enclosed spaces. Fans or air conditioning units can effectively moderate heat levels. Alternatively, when working outdoors, timing becomes crucial; applying coatings during the cooler parts of early morning or late afternoon ensures your project remains within optimal ranges.
However, it's equally important to recognize that temperature is just one piece of the puzzle; humidity levels require careful management as well. High humidity can interfere with curing processes and affect adherence, creating additional challenges during application. Preparing for your next significant project involves ensuring both temperature and humidity harmonize for effective results. Keeping this in mind allows you to navigate the intricacies of coating application more effectively, leading to greater success in your upcoming endeavors involving atmospheric conditions.
Managing Humidity Levels
The role of humidity in coating applications goes well beyond simple measurements; it significantly affects the final outcome. Too much moisture in the air can lead to complications, such as ineffective adhesion or even unsightly bubbles forming beneath the surface of your finish. It's essential to understand that the ideal relative humidity level is approximately 50%, where most coatings will perform best. Deviating from this standard can lead to delays in project completion and potentially compromise the quality of the work.
As studies suggest, for every 10% deviation from this 50% mark, you may notice drastic changes in how your coatings react. For example, at 70% humidity, water-based coatings could take up to twice as long to cure adequately compared to more optimal conditions. That means if you're on a tight timeline or working on a client project, you could find yourself in a real bind. To combat high humidity levels, especially in enclosed spaces where airflow may be limited, employing dehumidifiers can make all the difference. They work diligently to reduce moisture levels while preserving the integrity of surfaces prepped for coating. Conversely, when the air is too dry, adding humidifiers ensures there's enough moisture present for coatings to settle properly without cracking or peeling.
So how can you ascertain that you're maintaining an appropriate humidity level? A simple hygrometer can measure indoor relative humidity and guide your decision-making before starting any coating application. Additionally, local weather reports play an integral role in planning your projects in non-climate-controlled environments. With foreknowledge of impending high humidity days, you can adjust your schedule accordingly.
While it's clear that managing humidity is vital for successful coating applications, surface preparation holds equally significant importance for optimal results. Let’s turn our attention to effective techniques for getting surfaces ready for coating.
Surface Preparation Techniques
The condition of the surface to be coated significantly impacts the effectiveness of any coating you apply. A clean, well-prepared surface promotes better adhesion and prolongs the life of the coating itself. The first thing to do is clean the surface thoroughly. Start by removing debris; whether inside on walls or outside on decks, using a broom or vacuum will clear away loose dirt and dust that can easily interfere with adhesion. Overlooking this step can lead to major headaches later.
Once cleared, proceed to degreasing. Applying a suitable degreasing agent is essential because it removes oils and residues that would otherwise cause poor bonding. Allow this degreaser to sit for about 5-10 minutes before rinsing it off to ensure maximum effect. This step cannot be overstated; without cleaning off grime, coatings can bubble or peel off like paint during a heat wave. Ensure the surface dries completely after cleaning; moisture left behind can act as an adversary when it comes to adhesion. Many find that moisture control yields notable improvements in their projects’ outcomes. Having cleaned your surface meticulously, the next step is to address its texture through sanding and smoothing.
Sanding and Smoothing
After ensuring cleanliness, lightly sanding the surface prepares it further. Think of sanding as giving your surface a light “scrub,” gentle enough that it remains intact while enhancing its texture for better bonding. Aim for a roughness that feels slightly gritty to the touch—this is where coatings will grab on and hold fast. For example, when applying epoxy on garage floors, proper sanding is an indispensable step. Without creating this key texture, users often report issues like peeling long after application, which could have been easily avoided with proper prep.
Beyond enhancing adhesion, sanding helps achieve an even finish upon application. Not only should you sand down high spots and imperfections for aesthetics, but you’ll also want to maintain consistent techniques across larger areas so it looks uniform after the coating is applied. If working on outdoor surfaces, consider power washing as part of your cleaning routine; it's effective, but ensure they dry completely afterward before proceeding with any more steps. Equipped with these surface preparation techniques, you're poised for success in your coating endeavors, seamlessly transitioning into understanding how environmental variables impact drying and curing processes.
Drying and Curing Influence
Drying and curing are intricately linked but represent different phases in the life of your coating. When we think of drying, what comes to mind is the simple process where solvents or water evaporate from the surface, leaving behind a layer that feels dry to the touch. Conversely, curing involves chemical reactions that solidify and harden the coating, making it resilient to wear and tear. Exploring the factors influencing curing can further guide our approach to effective use of coatings.
Factors Affecting Curing
To ensure that your coating fully cures as intended, maintaining stable temperature and humidity levels throughout this process is paramount. Ideal conditions generally recommend temperatures between 50-70°F with relative humidity around 50-70%. High humidity can prolong drying times, while excessively low humidity instantaneously increases evaporation rates, posing risks of an incomplete cure.
Additionally, certain fast-curing agents can be beneficial; however, always align their use with the manufacturer’s guidelines to avoid compromising the quality of your application. Remember that rushing through the curing process may seem tempting when time is tight; nevertheless, hasty measures will often result in subpar finishes or premature failures. Think of curing as an investment—taking your time will yield a more durable and aesthetically pleasing coating.
By respecting these nuances around drying and curing processes while applying coatings, not only do you save yourself potential headaches down the road; you also enhance the longevity and integrity of your work considerably. This foundation sets the stage for exploring key strategies that maximize application effectiveness.
Effective Application Strategies
The method of application plays a pivotal role in achieving the optimal finish of your coating, and for good reason. Imagine pouring over your favorite book only to find it smudged and unreadable—this is what can happen if you don’t approach the coating process with care. The right techniques can make all the difference, ensuring that every coat not only adheres properly but also looks stunning.
- Use of Tools: Choosing the right tools is akin to selecting a series of brushes for a painter; each serves a specific purpose and contributes toward the final masterpiece. For broad surfaces, high-quality foam rollers are invaluable as they minimize bubbles and provide a smoother finish. Alternatively, brushes are ideal for edges, where precision becomes paramount. When it comes to hard-to-reach spots or intricate details, spray guns excel by allowing for even distribution of product without excessive build-up. It may also be beneficial to experiment with various tool types on small areas before committing to larger projects. This practice allows you to gauge what works best with the specific coating product you're utilizing, leading to greater efficiency and enhanced results.
- Layering Wisely: Apply your coating in multiple thin layers—a technique that fosters both durability and aesthetic appeal. Beginning with an even base coat creates a foundation upon which subsequent layers can securely bond. It’s important to allow each layer to dry thoroughly before proceeding; skipping this step is akin to trying to build a house on sand—a shaky proposition at best. With each added layer, you're not just enhancing visual depth but also fortifying the surface against wear and tear. Pay attention to environmental factors such as humidity and temperature during application. Conditions ideal for drying will ensure that each layer sets according to plan rather than presenting unexpected challenges down the road.
- Follow Manufacturer's Instructions: Adhering strictly to the manufacturer’s guidelines cannot be overstated; these instructions are your roadmap to success. Each coating has specific mixing ratios and recommended application techniques designed to optimize performance. For example, adding extra solvents in an attempt to thin the mix might seem like a good idea but can lead to severe faults like cracking or poor adhesion down the line.
Through diligent adherence to guidelines, not only do you enhance your chances for long-lasting finishes but you also build trust with clients when they see that high standards are maintained. By applying these effective strategies thoughtfully and keeping abreast of technological advancements within the industry, you'll set yourself up for not just immediate success but also long-term triumphs in your coating projects.
In summary, mastering the application process not only leads to superior results but also builds lasting trust with customers. Your commitment to excellence in coating applications sets a benchmark for quality craftsmanship in the industry.
Top-Notch Ceramic Coating Services in Marietta, GA
Keep your vehicle’s paint looking flawless with LeJeune Ceramic Coating & Paint Protection’s expert ceramic coating services in Marietta, GA. Our advanced coatings create a hydrophobic barrier that repels dirt, water, and contaminants while enhancing gloss and depth. With long-lasting durability and UV resistance, your car stays protected from fading, oxidation, and everyday wear. Whether you want effortless maintenance or a showroom-quality shine, our team ensures a perfect application tailored to your needs. Get in touch today and experience the difference of professional ceramic coating!
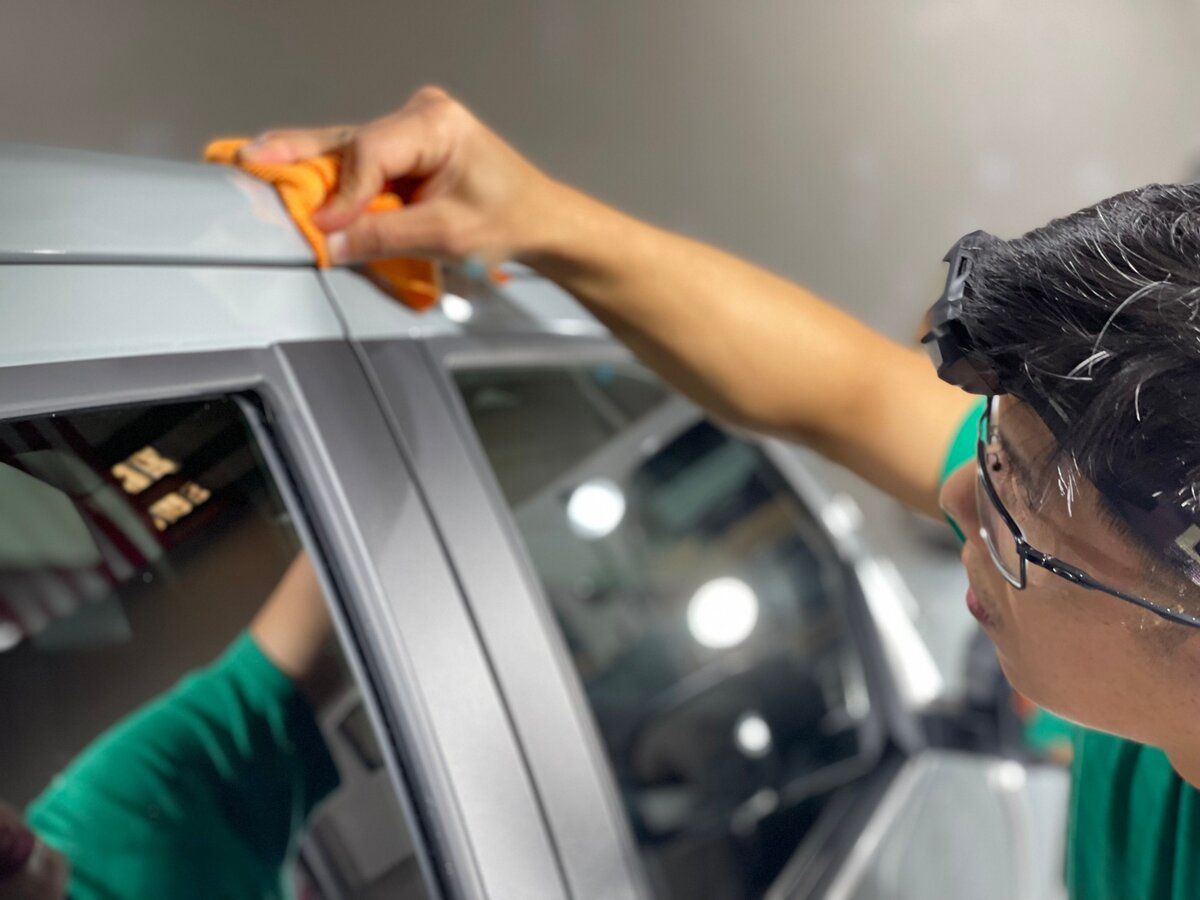
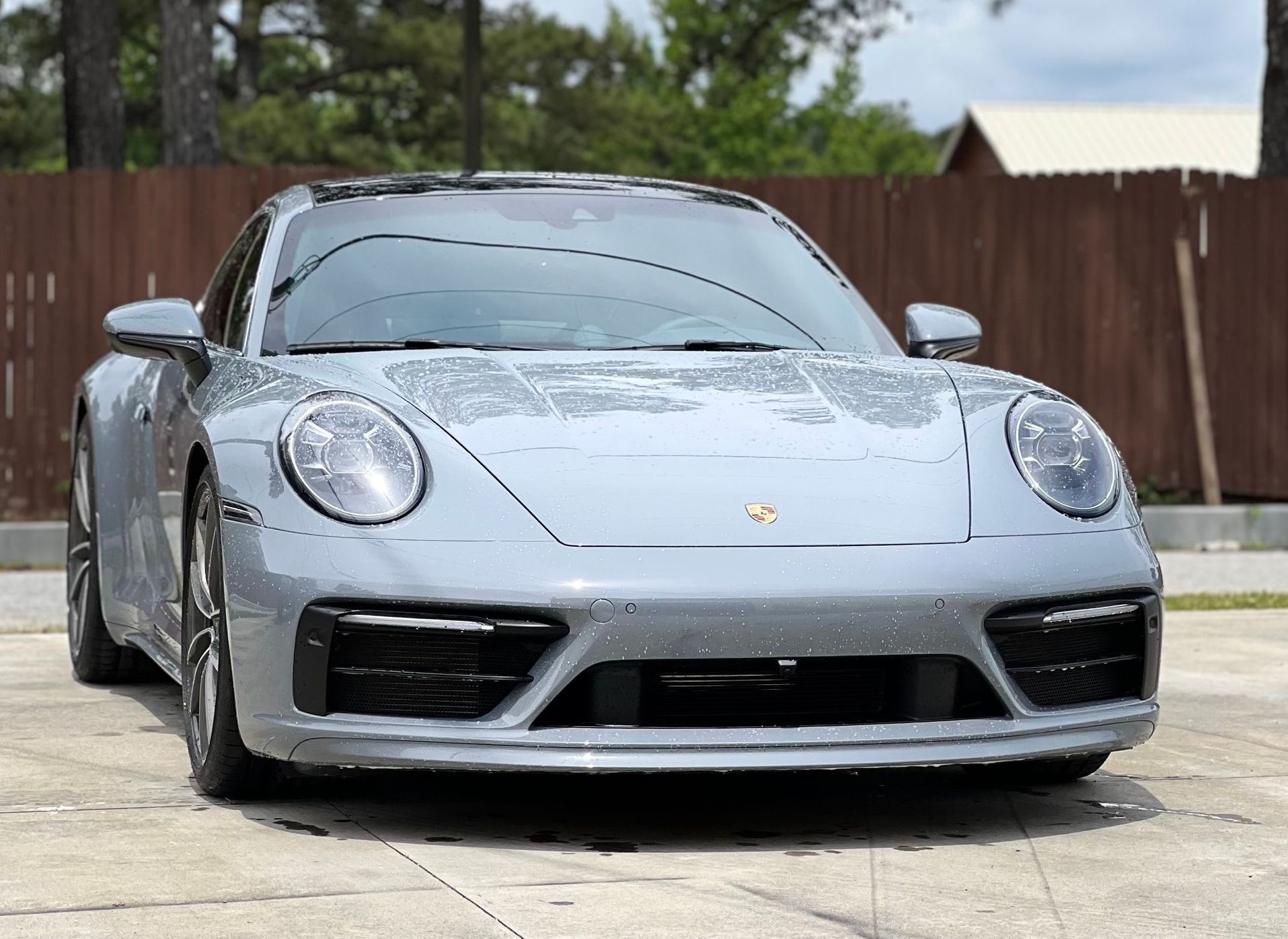
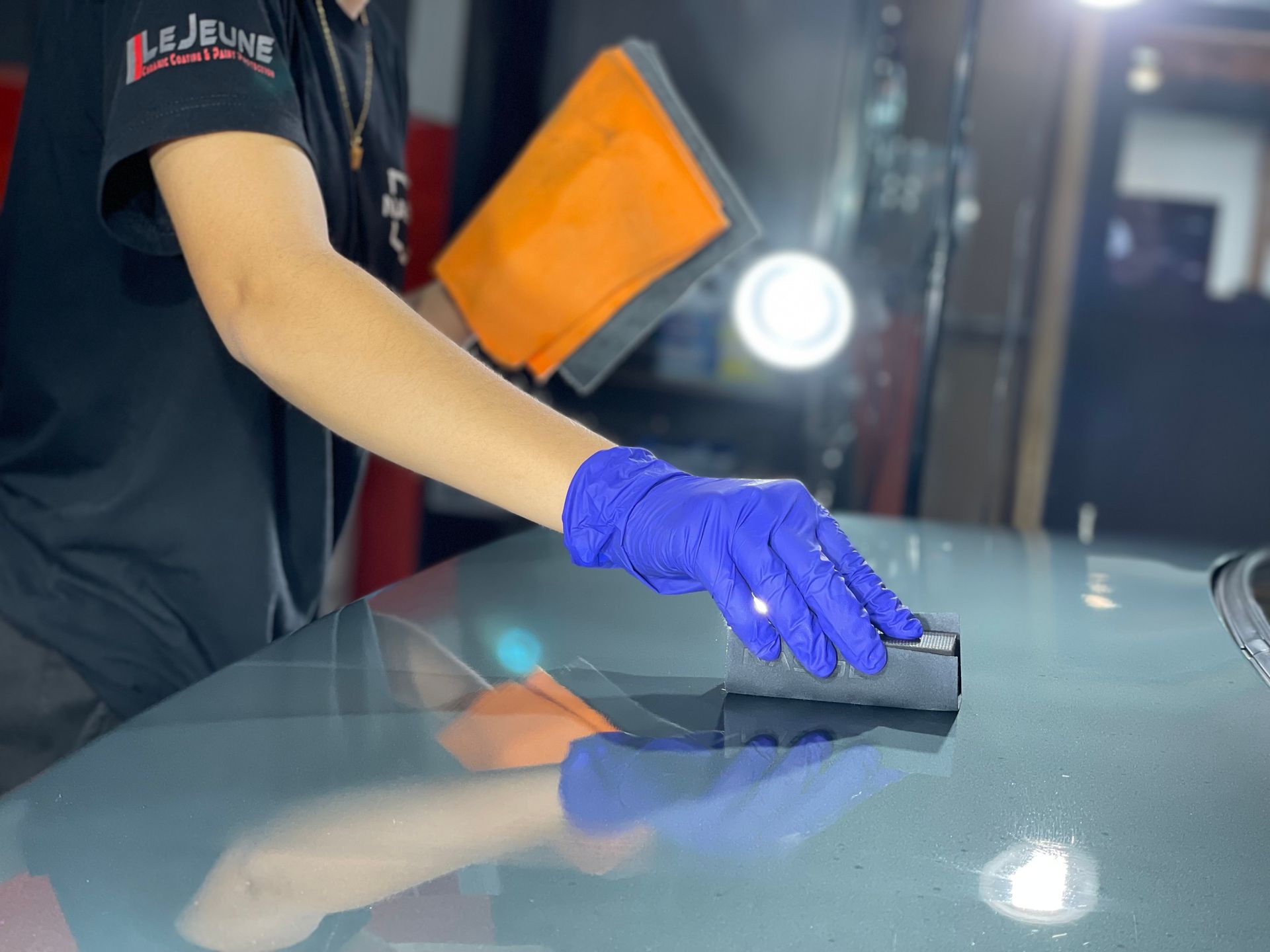